How Important is the Strength-to-Weight Ratio of Metals?
Contents
Understanding the strength-to-weight ratio is helpful when working with different types of metal because it affects what they can be used for, and how they can be formed.
This article goes over what strength-to-weight ratio is, what it means for choosing the right type of metal to work with, and what the limitations of some common metals are.
What is Strength-to-Weight Ratio?
By the most simple of definitions, the strength-to-weight ratio of a given material is the strength of the material divided by the mass (also commonly referred to as weight, on planet earth) of the material.
To be more exact, specific strength is a material’s strength divided by its density. For the sake of simplicity let’s refer to this property as the strength-to-weight ratio.
Application
In sheet metal forming and stamping, the product designer must understand the various options for material choice, and the strength-to-weight ratio is often a significant factor. In most applications, especially automotive and aerospace, the desire is to have a very strong material with as little mass (or weight) as possible.
For example, materials such as aluminum, titanium, and magnesium are often chosen because of their high strength-to-weight ratio. If the mass is not a huge concern, then steel may be chosen to achieve the same strength, but at a weight penalty.
However, strength and mass alone may not be the only factors to consider. When choosing a material for a sheet metal part, there are numerous other factors to consider, such as:
- Cost of raw material
- Corrosion resistance
- Weldability (for assembly of multiple parts)
- Ease of manufacture and supply in quantity
The cost of raw material can easily rule out (or limit the use of) materials such as aluminum and titanium. Every engineering choice is a compromise between ideal and cost-effective. If cost was no consideration, then every car chassis on the road today would be made from an exotic material such as titanium or carbon fiber. Cost is a huge consideration alongside strength to weight ratio.
For this reason, many high strength sheets of steel have been developed (since high volume steel production is relatively cost-effective) and are often used in place of aluminum and other higher-cost materials. Also, it is not uncommon to use a selection of different materials, in the context of a large assembly of sheet metal parts.
For example, the Tesla Model 3 moved away from a nearly 100% aluminum chassis. According to electrek, The Tesla Model 3 has only a small portion of aluminum, with a mix of various strength steels making up the majority of the Model 3 chassis and body. This is because of the consideration of cost as well as the strength to weight ratio of the entire body assembly.
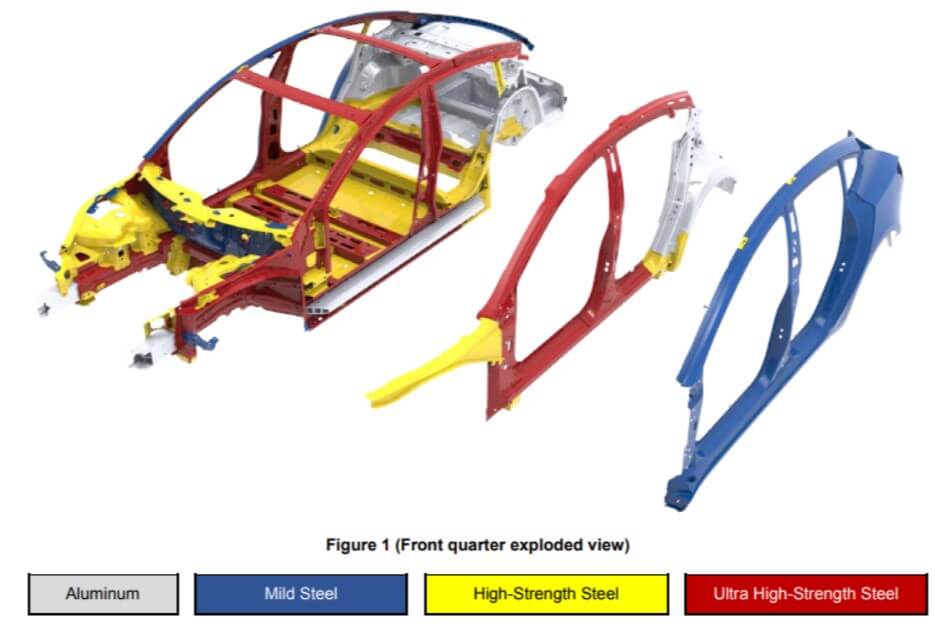
Source: https://electrek.co/wp-content/uploads/sites/3/2017/08/5dyii0y.png
How does simulation help designers choose the correct material for their sheet metal designs when considering the strength-to-weight ratio?
When a sheet metal part designer chooses a material, they must consider the grade and thickness in order to achieve the desired stiffness or strength of their product. Some grades of steel (or aluminum or titanium, etc) are easily formed whilst other grades present enormous challenges, with respect to forming the material into the desired shape.
Generally speaking, the higher the strength of the sheet metal material, the more difficult it is to form successfully. High strength materials often present great opportunities to save weight, but careful engineering must be included to ensure the specified material can be successfully formed into the desired product shape, alongside other side effects such as spring back.
Product design must often be adjusted to work with high strength-to-weight ratio materials. Small radii and features that might form successfully in mild steel, may not form in high strength steel or aluminum.
AutoForm Forming R8 incremental simulations consider the exact material properties and tooling geometry in every forming step, to accurately simulate the expected outcome of forming a high strength-to-weight ratio material.
Contact Metal Forming Experts
StampingSimulations has been in the sheet metal forming business for years, we can help you decided what metals are going to be best for your project. We factor in the cost and longevity of the metals to ensure a quality outcome. Contact us today with any questions you have.