Identifying and Resolving Manufacturing Defects Through Detailed Simulation
Manufacturing defects can result in low-quality products, which in turn may be catastrophic, depending on the industry you operate in. The good news is that intricate simulations are now available, allowing companies to identify the source of the defects and provide solutions without having to go through a trial-and-error process. In this article, we discuss the benefits of using simulations to identify and address metal forming manufacturing defects.
We have spoken many times about splits, wrinkles, and springback. In the case of outer skin panels, the surface finish is paramount and must be perfectly wrinkle-free and pass stringent quality inspection criteria. Therefore, predicting and finding defects in outer skin panels or any sheet metal part that requires a high-quality finish for exterior presentation is a whole other topic in itself.
The example shown here is a more severe case of surface quality issues caused by lack of stretch in the material during the draw forming process. This panel shows “loose” material that does not pull tight and becomes “gathered” even though the material does not fold over itself or “wrinkle”. In fact, in simulation, we inspect for this type of defect before the bottom dead center of the press stroke, because closing the tooling 100% can often hide the defect—the sheet may appear to be “OK” once the tooling bottoms out.
Apart from inspecting the FEA mesh visually to find the defect, we can also call out stress/strain values and plot a color map that shows where these defects are expected numerically. There are numerous tools to find and highlight defects on skin panels within the simulation environment.
More importantly, how does one solve and counteract such a defect? The key requirement is to stretch the material in all directions as much as possible. This often requires the use of draw beads to deliberately and positively induce stretch in all areas of the part. Just about every skin panel (almost without exception) requires draw beads to achieve the high-quality surface finish required.
Companies that decide not to use draw beads in these situations, often find themselves polishing away the metal thickness instead! Even though the product may be a polished finish, the underlying problem is still evident.
The apparent cost saving by not using draw beads and relying on the polishing process does not remove the defect. The surface quality is not built into the process and the end result is less than perfect.
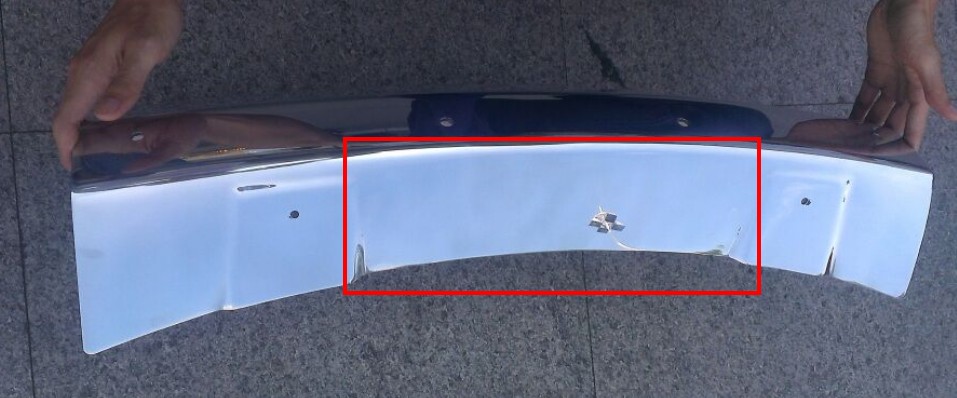
The “surface looseness” is still evident after polishing. No draw beads were used.
Needleless to say, the same problem is found easily with simulation and can be corrected with a stretch forming process, including draw beads. It’s true this method creates more scrap and more investment in tooling upfront, but how does that compare to the cost of producing defective parts?
Want to Learn More?
StampingSimulation specializes in all kinds of metal forming simulations, including those that will anticipate and avoid manufacturing defects, saving you time, material, and money in the long run. Contact us today to learn more about what we can do for you and your metal forming project.