Elon Musk – You Are Wrong About Forming Stainless Steel – Part 1
Contents
Unless your head has been buried in the sand, the recent reveal of Tesla’s Cybertruck unveiled “Ultra-Hard 30X Cold-Rolled stainless-steel” as the primary material for the complete “exoskeleton” of the entire vehicle. Although the details of the entire bodywork is not clear, Musk stated that the panel thickness was 3mm and bulletproof to a 9mm handgun. Musk went on further to also state that the new stainless alloy (developed by Tesla for their starship rocket) could not be formed into any shapes because “it would break the stamping press”.
“We were able to make the skin out of thick ultra-hard stainless steel…..it’s really hard….we’re going to show you just how hard” Elon Musk
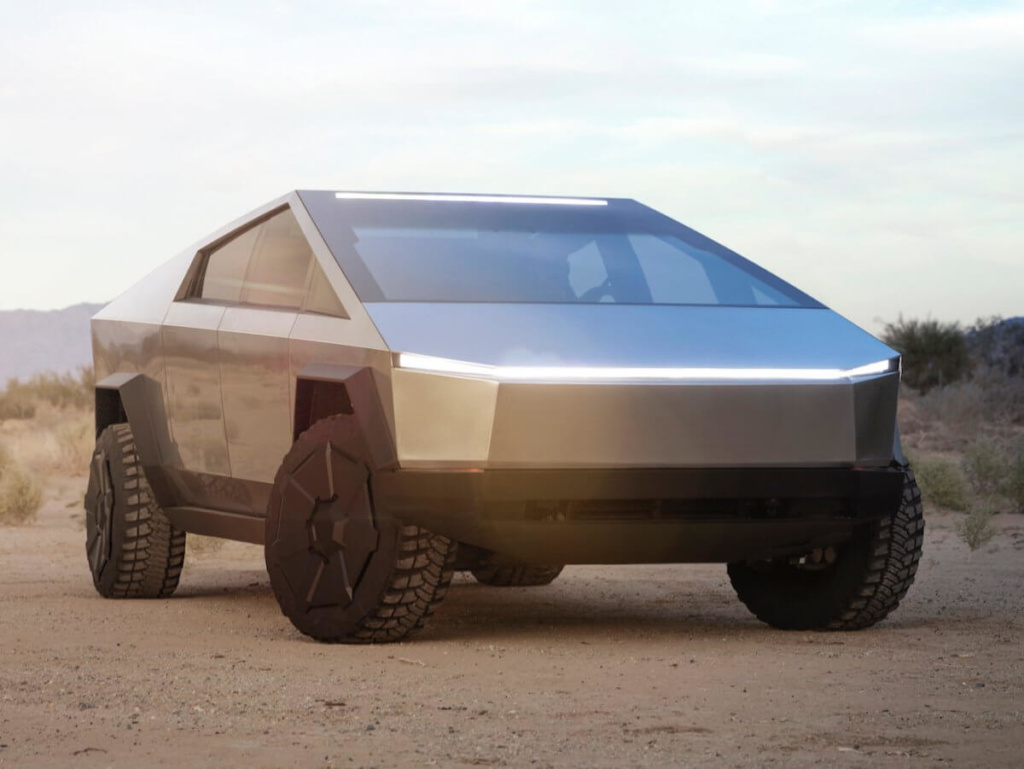
The Cybertruck uses what Tesla calls “Ultra-Hard 30X Cold-Rolled stainless-steel.” This material is supposed to be superior to stainless 304. Source: Business Insider
Is Forming “Hard” Stainless Steel Possible?
The first issue a sheet metal engineer has with this statement is the constant use of the word “hard”. The correct engineering term would be “strong”, as in strength or yield strength, to be more exact. A material that is “hard” is not necessarily strong, and a “hard” material may indeed have lower tensile strength than a “soft” material. The point is, the word “hard” (or soft) is the wrong way to describe the strength of a material.
Hardness, in fact, is a separate property on its own and is measured on a hardness scale, which is entirely different from strength.
Granted, Elon Musk is a highly skilled engineer and probably entirely aware of these engineering facts, and perhaps is simply complying with common industry nomenclature, in the same way, non-engineering folk interchange lbs-ft with ft-lbs when referring to torque (the former is correct, the latter is technically wrong).
So let’s give Elon the benefit of the doubt with respect to the incorrect use of the word “hard”, technically speaking.
“Reason Cybertruck is so planar is that you can’t stamp ultra-hard 30X steel, because it breaks the stamping press.” Elon Musk
Are you sure Elon? Various automotive components have been stamped from “ordinary” stainless steel for decades. These include exhaust components (usually 400 series stainless steel), as well as some cosmetic components such as bumpers and aftermarket accessories (usually 300 series stainless steel).
Could the new SpaceX “Ultra-Hard 30X Cold-Rolled stainless-steel” be so strong (not hard) that it would literally break the stamping press? I don’t think so.
Why it Wouldn’t Break the Stamping Press
“30X” most probably refers to a 300 series grade of stainless steel alloy eg: 304 is common. The “X” in “30X” probably denotes the new alloy that SpaceX has developed. Another possibility is that the “30X” actually means 30 times, as in, the new alloy is cold rolled 30 times over, to work strengthen the material (also known as work “hardening”) to improve it’s mechanical properties. It’s not clear which meaning is correct, without input from Elon Musk or his SpaceX engineers.
How Stainless Steel Forming is Achieved
Let’s examine both assumptions.
If the new material is indeed a 300 series stainless steel, that has been cold rolled, then the maximum “benefit” the cold rolling can give the material is to increase its Yield Strength to almost equal its Tensile Strength. Thus, in the case of 300 series stainless steel, typical figures look like this:
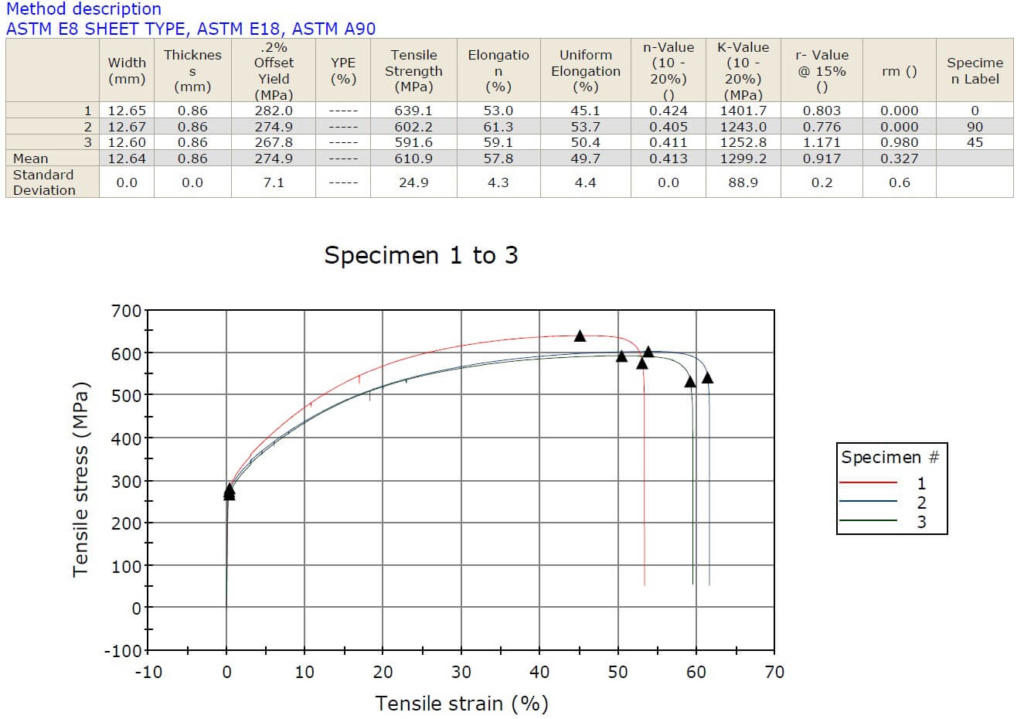
Typical mechanical properties for stainless steel 304 – uniaxial tensile test from a real-world sample
In summary, we can see that Yield Strength is about 275 M Pa and Tensile Strength is about 611 MPa. If the material were to be cold worked to improve its Yield Strength, the maximum possible strength is 611 MPa. Cold working or cold rolling cannot improve the base material beyond its ultimate tensile strength. To do this would require a significant amount of cold work to be done on the material. Perhaps this is why the “30X” could refer to cold rolling the material 30 times over, and not to a 300 series alloy.
After all, it’s a “new” stainless steel alloy developed by SpaceX, right?
Thus the real question is (if the above assumptions are correct), will cold-rolled stainless steel with YS = TS = 611 MPa break the stamping press?
Answer: No, assuming the press is correctly sized for the part. The part will fail (split or crack), not the press.
The part cracks or split during the attempted forming operation, because the material that is cold worked to the point of its Tensile Strength, has no ability to stretch or form. If the material is cold rolled or worked to its maximum, any additional cold work (ie: forming in a press) pushes the material past its Tensile limit and it fails (cracks).
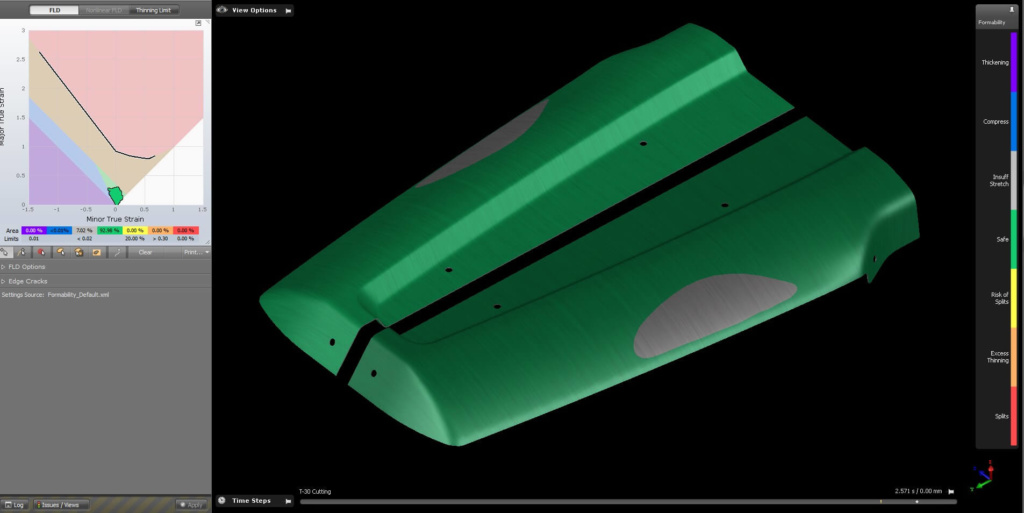
With the help of StampingSimulation, these two parts were formed successfully from stainless steel 304. Press requirements were 150 tons. The press did not break. The resulting strength of the panel is much greater than the original material, due to cold work during forming.
It is not uncommon for large automotive stamping presses to be in the 1000s of tons. Even 5000 tons. That’s a lot of tonnage to stamp even the strongest materials. In fact, the automotive industry already stamps very high strength materials, some with Tensile Strengths greater than 1200 MPa. At even higher strengths, heating is used to form ANY strength of material into ANY shape. This is already common practice, although it comes at an increased cost.
In Conclusion
So Elon is wrong about forming stainless steel. In addition, Elon has specified 3mm thick stainless steel, which GREATLY increases forming tonnages required. Typical automotive skin panels are just 0.65mm thick, so 3mm thick is a huge increase in material mass and means the press has to be many times larger to stamp thicker 3mm material successfully.
One must wonder, would a 3mm thick high strength steel door perform the same as the 3mm “Ultra Hard Stainless Steel” vs the sledgehammer test? Probably yes, given that high strength steel during forming is also cold worked and strengthened in the exact same way as cold rolling stainless steel.
Thus, Elon should have stated “forming a complete exoskeleton using our new 3mm 30X Ultra Strong Stainless Steel will break our stamping press……so we decided not to form or shape the panels”
Clever marketing? OR genius engineering?
More to follow in part 2 next month…….
In the meantime, if you have any questions about sheet metal or stainless steel forming give us a call.