Metal Forming Simulations: Evaluating the Past, Present, and Future
Contents
The introduction of metal forming simulations completely revolutionized the manufacturing industry and all other verticals associated with this trade. That being said, these technologies have come a long way in a short period of time—they are set to make significant advancements in the next few years as the techniques used become more and more accurate. We evaluate the past, present, and future of metal forming simulations and showcase the most important benefits they have to offer.
Past
I personally became aware of sheet metal forming simulation technology as a graduate engineer at Toyota Motor Corporation Australia in the early 2000s. Having graduated as a Mechanical Engineer (BEng Mech & Space – with honors) in the year 2001—I was fortunate enough to be accepted into the graduate program with Toyota in Melbourne, Australia. Although vehicle mass production in Australia is now 100% obsolete (all OEMs have withdrawn from manufacture in Australia), at that time in the early 2000s there were four OEMs (Toyota, Ford, GM, and Mitsubishi) all manufacturing in the southern states of Australia. The industry was highly skilled and alive and well—at that time!
My first position at Toyota was with the Quality Engineering department, and I was one of two engineers responsible for the sheet metal part quality; more specifically—body parts. There were some 440 sheet metal parts in the body of a Toyota Camry alone, and some 60%+ of that content was local manufacture with locally sourced steel. Our goal was to fit 440 sheet metal parts together and result in a car body with the dimensional accuracy of +/-1.5mm.
In those early days, the biggest challenge for sheet metal parts was geometric accuracy, and repeatability—perhaps the same challenges we face today—as well as avoiding defects like wrinkles and splits. It was the early 2000s, and although simulation was technology was around for sheet metal parts, no supplier to Toyota in Australia was using it. Process design or planning was done by hand initially, before committing to a CAD-based tool design, and then tooling manufacture.
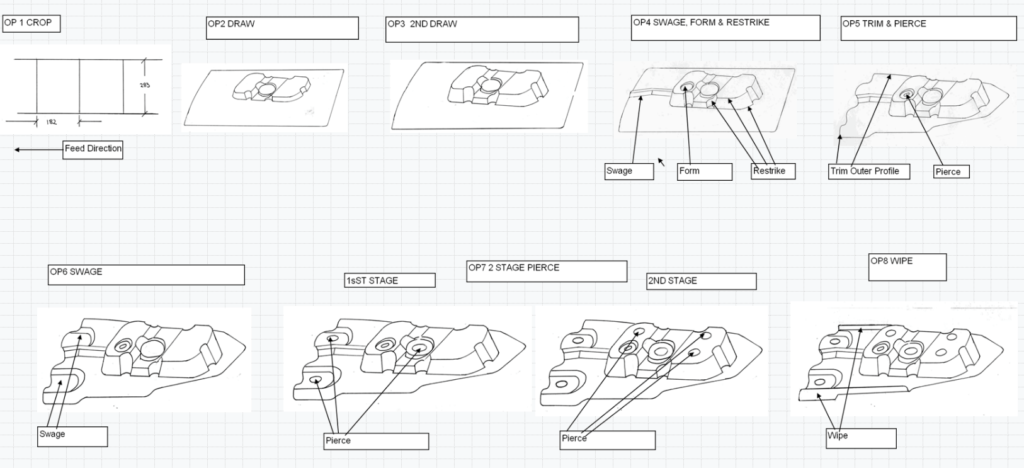
Will this process design result in an acceptable part, without checking in simulation?
The end result was hit and miss. Sure, some simple parts (and even a few not so simple parts) were no problem and passed all quality requirements, but these are not the parts I remember most. The more complex part shapes and higher strength materials are the parts that caused the most quality issues. Here are the common “reasons” given from manufactures to Toyota at the time, for un-acceptable sheet metal parts:
1. We made this part using this method last time but didn’t have these problems.
2. We only quoted three tooling stages, so we can’t fix the problem by adding more tools.
3. We wouldn’t have this problem if we changed the material.
4. We didn’t realize the blank needed to be larger.
5. We didn’t allow for extra material to use draw beads.
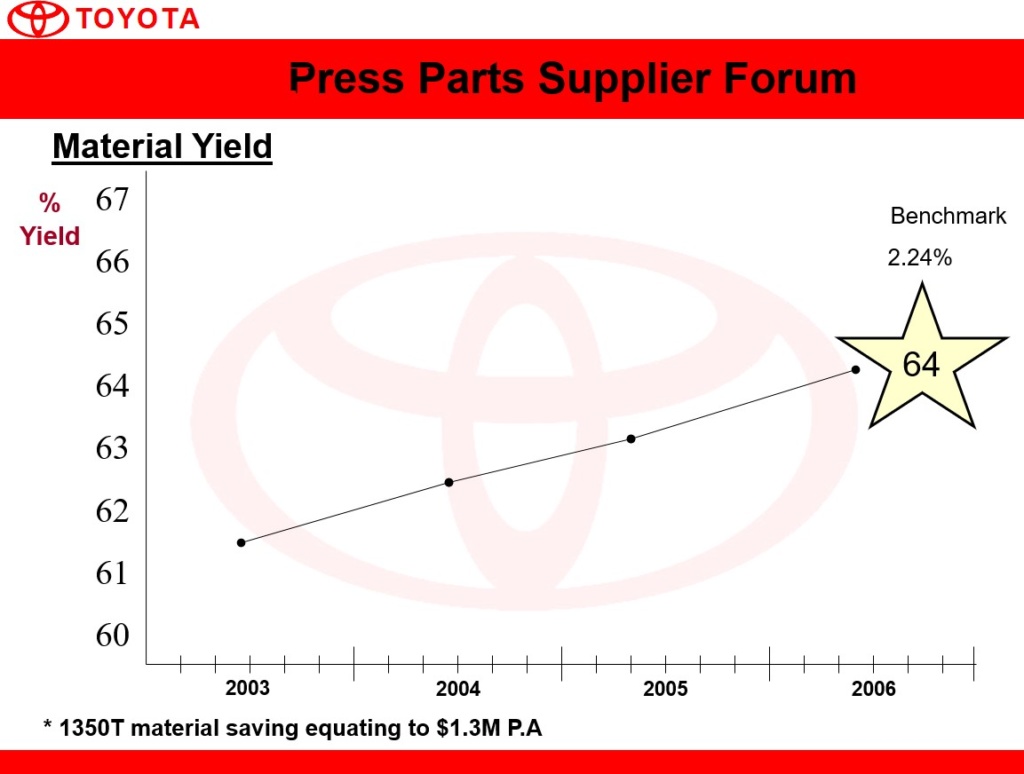
How do manufacturers meet stringent OEM material yield targets without simulation?
Present
This was the past. Sheet metal engineering without simulation.
The present-day simulation technology can definitively and accurately address all the problems described above at the design phase of a sheet metal stamping project before any commitment to supply of parts is even signed or budgeted. Companies who run simulation technology in-house use the technology on every part they quote so there are no surprises or unexpected outcomes when a tooling project begins.
Future
The future of sheet metal forming technology is exciting. What has become possible in the last 15 years from a desktop PC is phenomenal. AutoForm is a world leader in the continuous development of software in this space and often surprises with new features that assist tooling companies to compete on a global scale. StampingSimulation provides sheet metal simulation services using the AutoForm software. Contact us for more information or about a project you could you simulation technology on.