Assessing Springback Compensation Through Advanced Simulation
Contents
Springback can lead to disastrous consequences if it’s not taken into account during the manufacturing process. Understanding how springback works allows manufacturers to take measurements against it. In this article, we discuss how advanced simulations can help predict springback, allowing manufacturers to produce better design and prevent major flaws.
Advanced Simulation Can Be Used to Reduce Springback
Springback is considered to be one of the greatest challenges in today’s automotive industry, with increasingly high strength steels and aluminums being used to drive demands for higher fuel efficiencies and more safety. Compared to conventional steel, springback in modern vehicle manufacturing is a much more serious problem with today’s materials and the cost of springback compensation is a significant manufacturing cost.
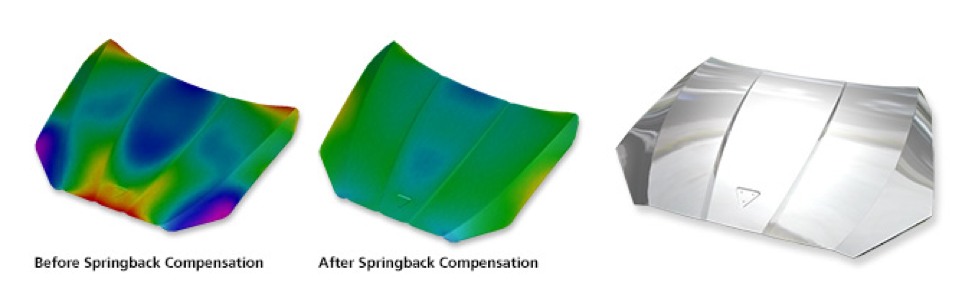
Springback compensation of a hood – before and after springback compensation in simulation.
Sheet metal forming simulation in the past has focused on analyzing splits and wrinkles (usually in the draw stage) but given the nature of the new high strength materials, the same focus has also been applied to geometrical accuracy. In addition to the draw stage, all stages of the stamping process must be carefully analyzed and considered to ensure springback compensation is verified during the car body engineering phase. Even with advanced computer simulation software, springback compensation is not an easy task and experience and knowledge must complement the computational power of simulation.
The most time and cost efficient way to apply springback compensation is during the tool design phase, before any tooling steel is machined, and before the real world tryout phase begins. Simulation calculates the expected (predicted) magnitude of springback and then applies adjustment to the die faces in the opposite direction. Such computations can be done in minutes or hours (not days or weeks) and each iteration of compensation is used as an input to the next simulation. To achieve the required tolerancing, a few optimization loops are required and this can be done as many times as needed in the virtual simulation world.
The end result after springback compensation using AutoForm simulation is a significant reduction in time and cost in both engineering and tryout phases.
Learn More
Interested in learning more about what is possible with advanced simulation software when reducing springback? Take a look at some of our case studies.
Further information on springback compensation at AutoForm:
Springback Feasibility for Efficient Compensation
Stamping Simulation Cuts the Number of Correction Loops